Hertha Metals has demonstrated a proprietary single-step pyrometallurgical process that converts low-grade iron ore directly into molten steel or 99.97% purity iron, without multiple stages or coal input. The continuous pilot plant in Conroe, Texas, has been operating at 1 tonne per day since late 2024. The process supports feedstocks such as sub-60% purity ores, fines and millscale—unlocking lower-cost raw materials and previously untapped US reserves.
Compared to traditional blast furnace or DRI-based methods, Hertha says its furnace is 30% more energy-efficient and can reduce emissions by over 50% using natural gas. When fueled with hydrogen, it enables up to 98% emissions reduction without hardware modifications. The furnace is modular and integrates into existing steel mills, with minimum viable scales as low as 500,000 tonnes per year.
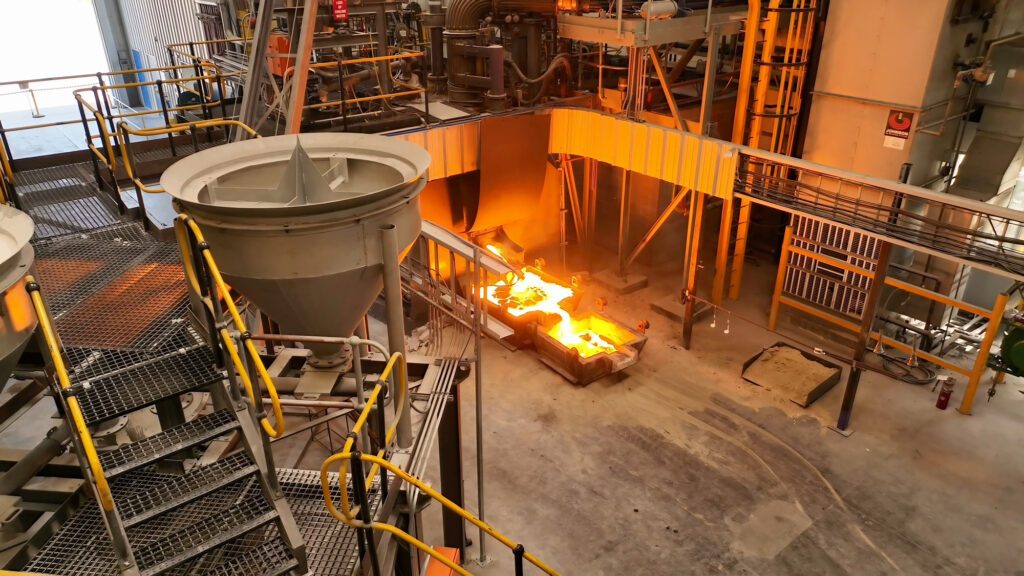
Backed by $17 million in new funding, Hertha plans to scale to 9,000 tonnes per year by 2026, targeting high-purity iron supply for NdFeB rare earth magnet production—a critical component of EV motors that is currently 90% import-dependent. Future plans include 500,000 tonnes/year steel production, reaching micro mill scale. The system supports tunable output—either crude steel or high-purity iron—depending on downstream requirements.
SEE ALSO: A closer look at rare earth permanent magnets
Source: Hertha Metals